
SCP Tech Brief: Concrete Curing
ACI 308R-16 Guide to External Curing of Concrete refers to curing as “Curing is an action taken to maintain moisture and temperature conditions in a freshly placed cementitious mixture to allow hydraulic cement hydration and, if pozzolans are used, pozzolanic reactions to occur so that the potential properties of the mixture may develop.” Spray-Lock Concrete Protection (SCP) products work by penetrating into the capillaries and voids left in concrete as bleed water exits. Once in the concrete, SCP products react with available alkalis to primarily form Calcium Silicate Hydrate (C-S-H), the same reaction product provided by cement hydration that provides most of concrete’s desirable properties. The reaction products formed fill capillaries and shut down liquid water transmission. The action works in the other direction as well, holding in water that would normally evaporate at early ages.
By making the water that would normally evaporate at early ages available for continued hydration, SCP products meet the intent of ACI’s definition of curing for maintaining moisture. Evidence of the continued hydration is drawn from the fact that SCP products improve concrete’s compressive strength and reduce drying shrinkage significantly, even when compared to moist-cured samples.
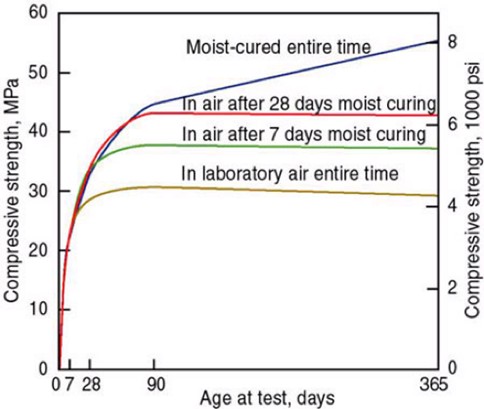
Figure 1: Effects of Curing on Concrete Compressive Strength Development (ACI)
According to ACI 308R-16, when determining the duration of curing, consideration should be given to the concrete properties that are desired in addition to compressive strength development. “For example, if both high compressive strength and low permeability are required concrete performance characteristics, then the curing needs to be long enough to develop both properties to the specified values. The appropriate duration of curing will depend on the property that is the slowest to develop.” By providing a permanent barrier to water migration, SCP products maintain curing indefinitely. In other words, the semi-evaporable and non-evaporable water continues to be made available for hydration until it is consumed, or an equilibrium state is achieved when SCP products are used. While membranes degrade over time, and water ponding methods cannot be continued indefinitely, the use of SCP products provides a continuous curing environment.
SCP-Treated Samples Performance over Moist Cured (% Increase) | |
---|---|
ASTM C39- Compressive Strength (28-day) | Up to 20% |
ASTM C157- Drying Shrinkage Reduction (28-day) | Up to 60% |
Concluding Remarks
ASTM C309 membrane-forming curing compounds were developed as a solution to the need for a time-saving alternative to water ponding. They are widely recognized as providing “adequate” curing but are not seen as equal to water ponding or water-saturated coverings. Additionally, SCP products become a permanent part of the concrete while membranes and water ponding are temporary. The objective of curing is to allow the concrete to meet performance parameters; SCP products produce those performance parameters at a rate equal to or better than moist curing.
Specification Guidance for Design Professionals
ACI 308.1-11 Specification for Curing Concrete section 1.1.2 Exclusionsallows designers to stipulate special curing procedures not covered by the specification. Because SCP product performance meet the intent of the specification by providing moisture retention, SCP products can be specified under this exclusionary provision.
Guidance for Flooring
Concrete to receive flooring materials is often subjected to water vapor emission rate using calcium chloride (ASTM F1869) and/or internal relative humidity (ASTM F2170) testing. SCP does not require either test for our flooring warranty for the following reasons:
- ASTM F1869 testing is not valid if any treatments have been applied to the concrete. Instead, we rely on ASTM E96 laboratory testing to establish a significant reduction in water vapor transmission by SCP spray-applied technologies.
- ASTM F2170 measures the internal relative humidity of the concrete. When SCP products are performing as expected, the readings on internal humidity meters will be higher than typically acceptable by flooring manufacturers. The reason is that the water than would normally evaporate is locked in, making it available for continued hydration.